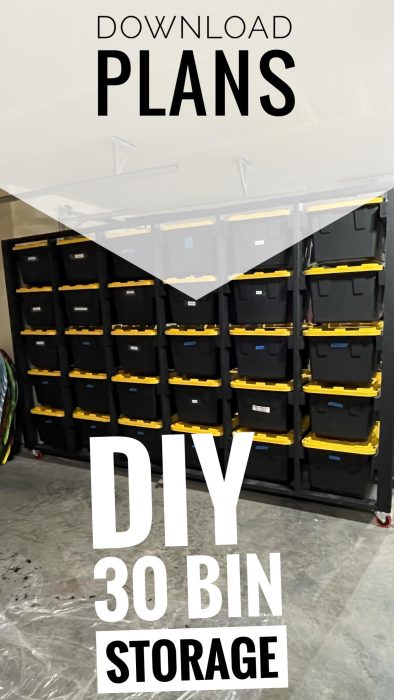
Salient Co-Owner Uses Viral Video to Raise Money for Family Promise of Gallatin Valley
Salient’s co-owner and inventor, David Yakos, created a DIY shelf project video that went viral on social media.
Read More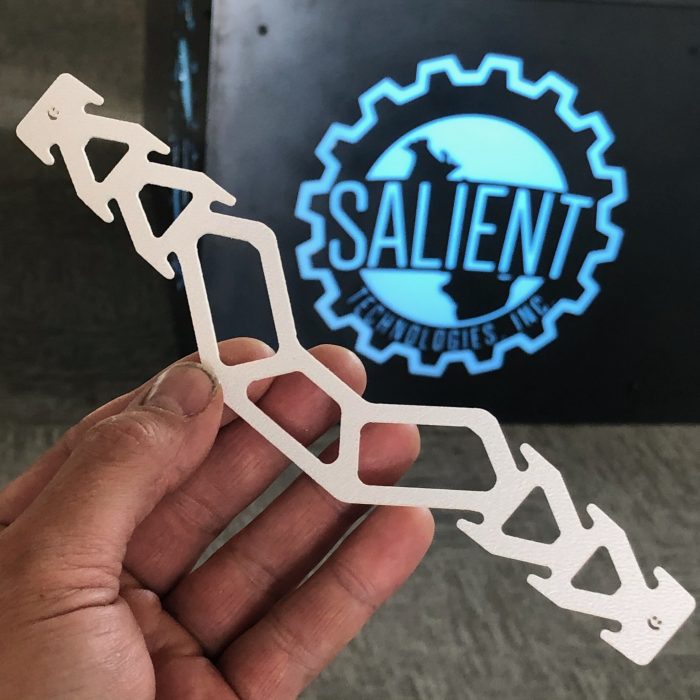
Happy Ears
Here at Salient Technologies, we love our laser cutter. It is well worth its keep for making prototypes. We love it even more when we can use it to help our local medical professionals!
Read More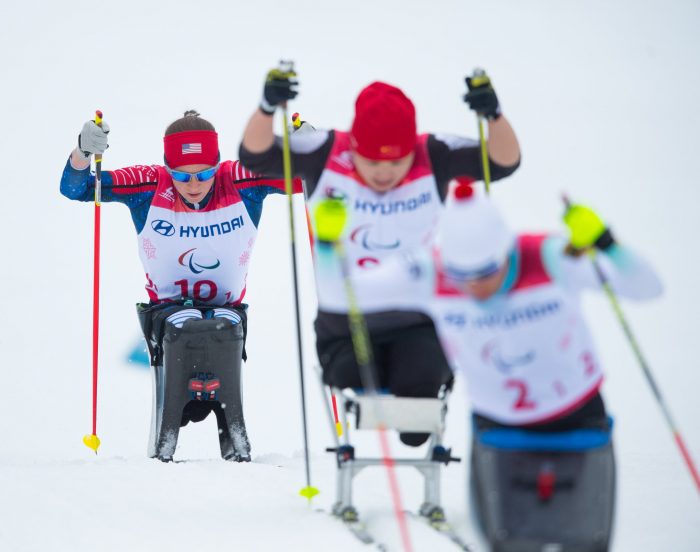
Innovation for Skiing
rface. The director of U.S. Paralympics Nordic Skiing reached out to Salient to develop a new interface between the seats used by Paralympic athletes and the newest Nordic skis.
Read More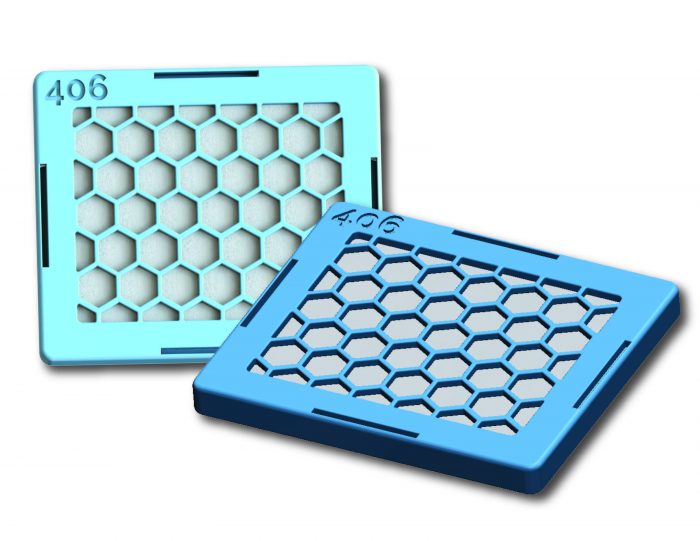
Innovation During a Pandemic
When the effects of COVID-19 began causing a shortage of personal protective equipment in America and Montana, Salient was quick to respond with design expertise. Salient designed an injection molded mask filter cartridge that is compatible with the standard 3M 6000 series masks to be mass produced in Montana.
Read More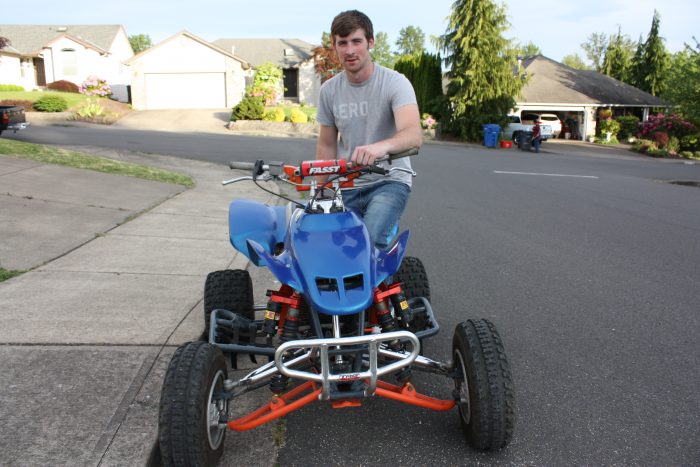
Building Frank
Here at Salient we are not only professional designers; we are also creators and makers. We have gone through the […]
Read More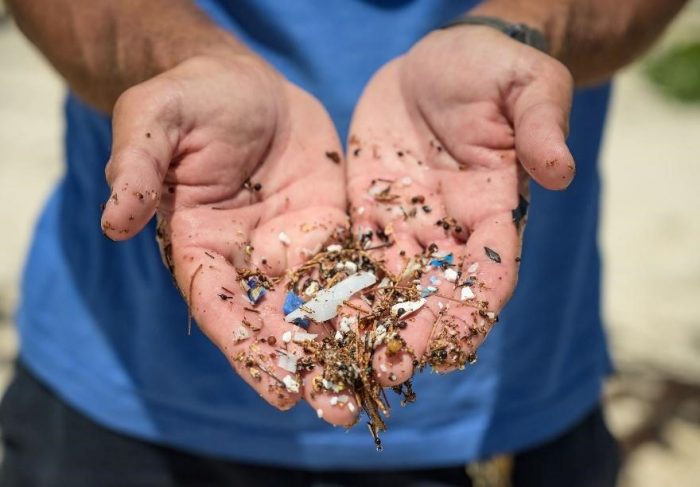
We’re all on the Same Boat
By David Yakos The phrase, “we’re all in the same boat” has new meaning for me after taking part in […]
Read More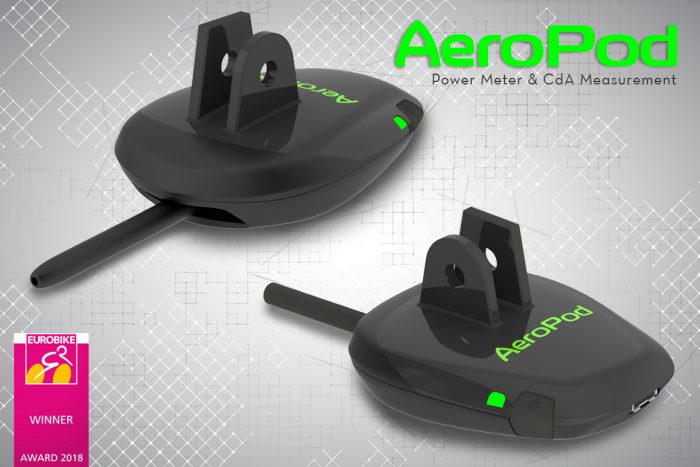
AeroPod – 2018 Eurobike Award Winner
The AeroPod by Velocomp (a Salient client for many years), won the prestigious Eurobike Award in the “Bike Components” category. […]
Read More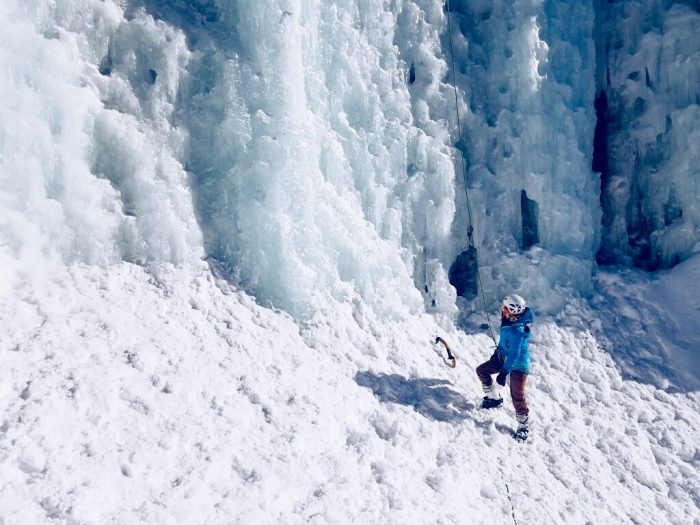
8 Reasons Getting Outside Makes You a More Creative Design Thinker
As a design and engineering consultancy, we feel living in Montana gives Salient a huge advantage in the realm of […]
Read More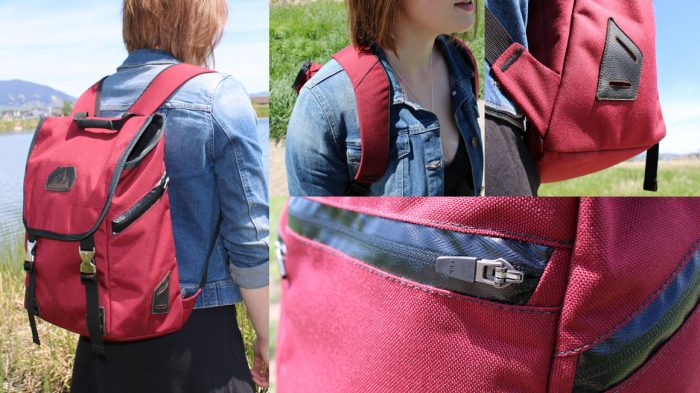
Process Practice Makes It Perfect
If you want to be good at basketball, it’s likely you’d spend hours dribbling, working on your layups, and shooting […]
Read More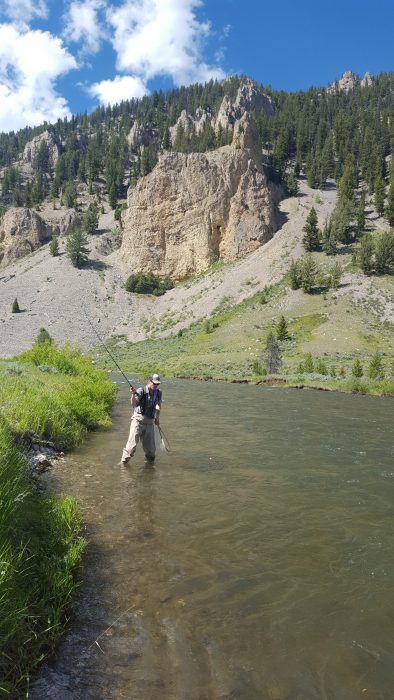
Extra-Special Overalls
Fly fishing is popular here in Bozeman, MT… Children named Madison sit in most elementary classrooms. Summer sees the university […]
Read More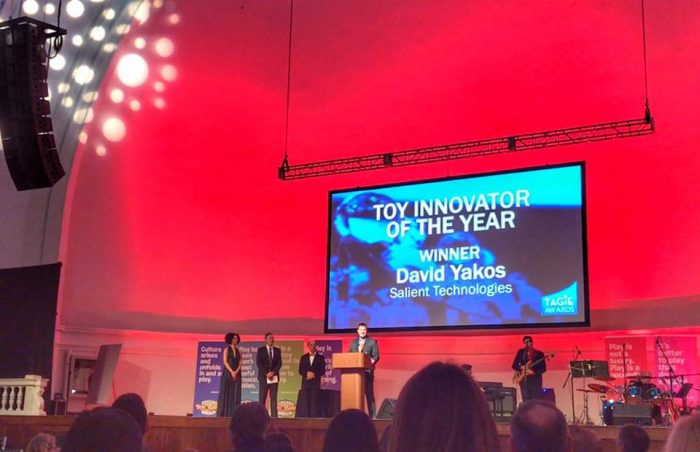
Salient 2016 Highlights
Another year has gone by, and here at Salient, we have lots to be excited about! Here (in no particular order) are […]
Read More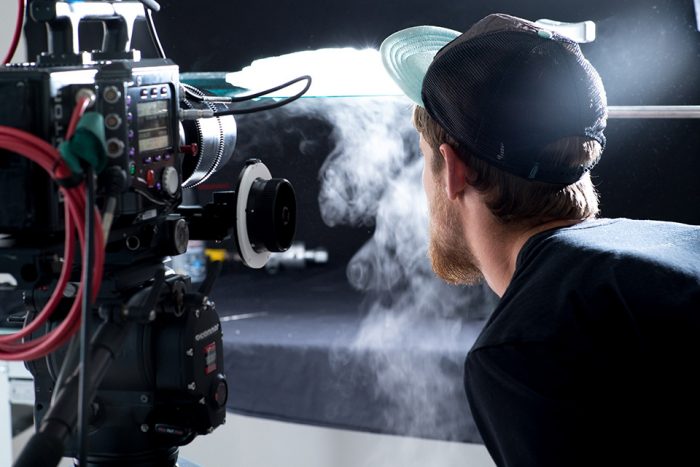
Salient-Helio Collaboration: 3D Printed Titles
Earlier this spring, Zach Johaneson of Helio Collective approached Salient about creating physical movie titles for use in-camera (instead of the typical […]
Read More