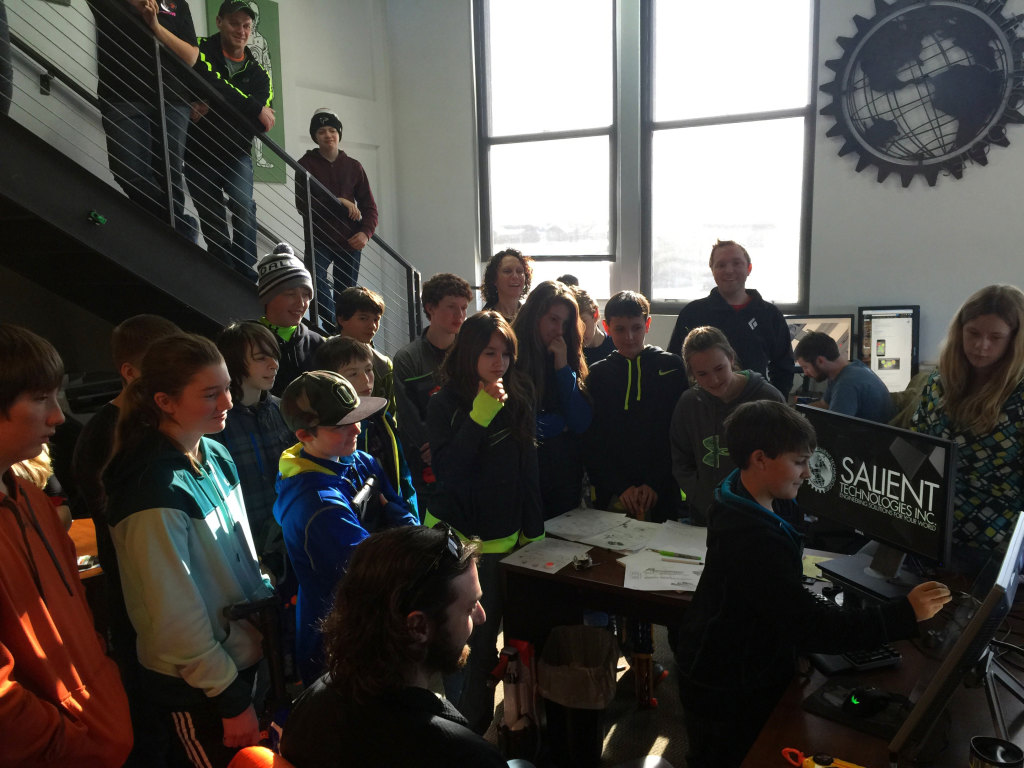
The Lincoln Middle School Students having a go at using the Wacom tablet during their tour of Salient
This last Friday and Saturday, I had the privilege of leading 20 junior high students and 10 high school students through the product design process here at Salient Technologies headquarters. The students traveled to Bozeman to take part in a FIRST (For Inspiration and Recognition of Science and Technology) Robotics competition. Picture an intense basketball tournament with dozens of teams, but instead of winning because you can put an orange ball through a metal circle, a team wins by completing complex challenges performed by a robot they built and created. The teachers coaching the team reached out to Salient for a tour and inside-look in aims to inspire kids to pursue careers in STEM (Science Technology Engineering and Mathematics), more specifically, design and engineering. It’s funny how things come full circle sometimes. Little did they, or we, know that the teacher leading the charge for the high school team was my first design/engineering/CAD teacher from nearly 20 years prior… a teacher who inspired me in the very same way.
The tour of Salient consisted of an inside look at the Design Process: what it looks like to take a product from imagination all the way to production. After working on thousands of products over the years, we were able to reference a handful of fun examples from NASA valves, to familiar household games like Yahtzee. We looked at industrial design, drawing in 3D CAD (and using Wacom tablets!), video animations, renderings, structural design and designing for manufacturing. It was just the kind of stuff I was first introduced to in the very same class this teacher was teaching in the mid 90s.
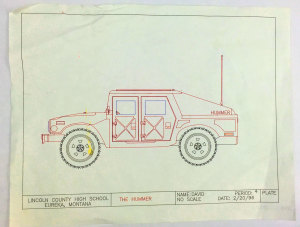
David’s first CAD file – a Hummer…go figure.
During the tour, I pulled out an old, yellowed drawing to share with the group. It was my very first CAD drawing – a side view of a Humvee drawn under the open-ended instruction of the very same teacher. It was drawn in 2D AutoCAD back when just printing in color was ground-breaking technology. I hung onto that simple drawing because it was an exciting discovery for me. It was where I first encountered a new tool that could help amplify my artistic and creative ability. It was the first time I got my hands on the same type of technology I now use almost every day in my exciting career.
On behalf of designers and engineers everywhere, I wanted to say thank you to the teachers who inspired creativity in the fields of science, technology, engineering and mathematics. In this specific case, Thank You, Mr. Ruble, for fostering a place of inspiration!