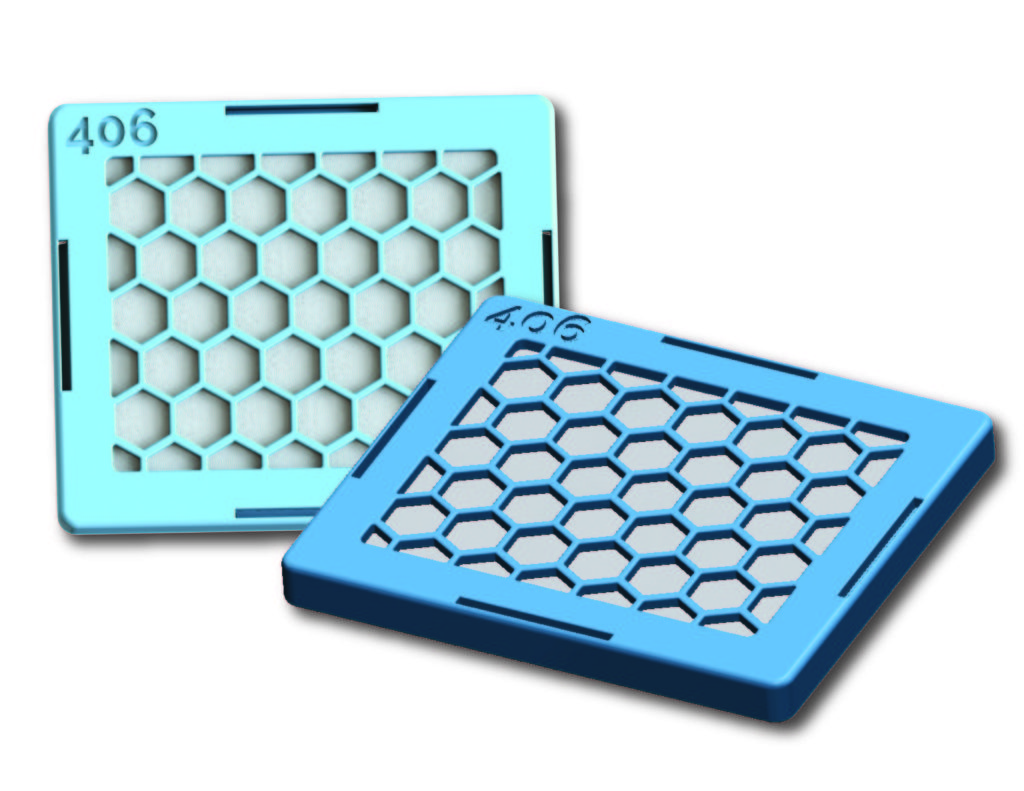
When the effects of COVID-19 began causing a shortage of personal protective equipment in America and Montana, Salient was quick to respond with design expertise. Salient designed an injection molded mask filter cartridge that is compatible with the standard 3M 6000 series masks to be mass produced in Montana. The team designed the mask in 3D CAD and then they 3D printed prototypes, which take about four hours each to 3D print. However, with injection molding, one filter cartridge can be produced in less than 60 seconds allowing for quick supply.
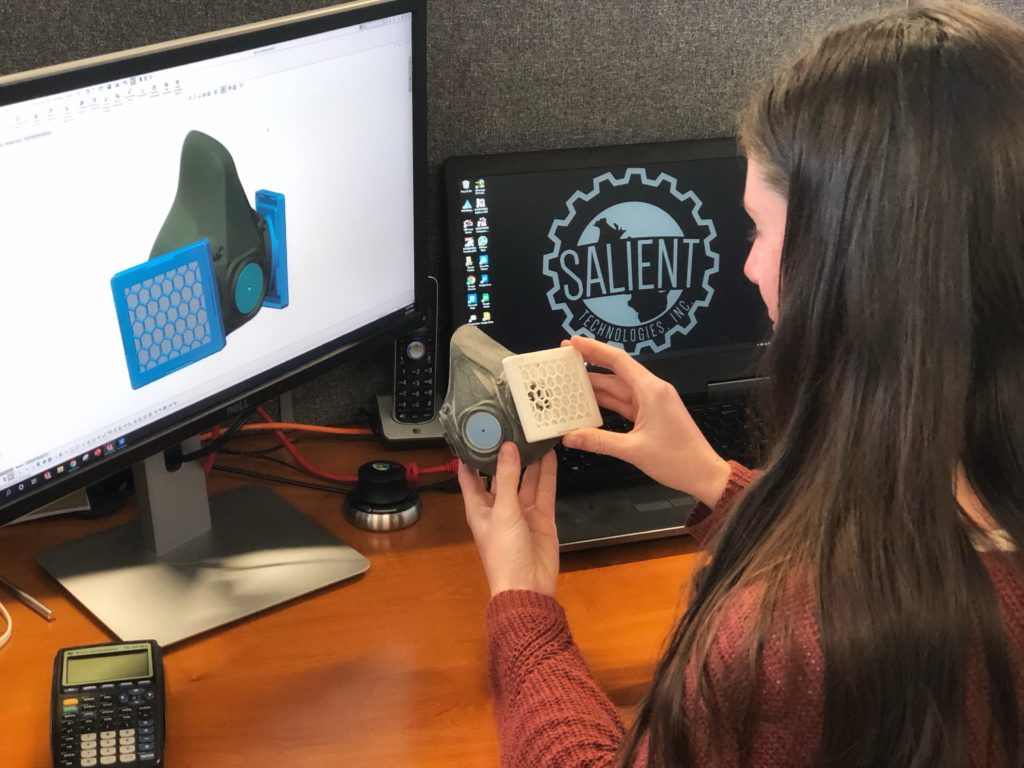
With a standard mask filter cartridge, it is difficult to sterilize the filter material inside. These cartridges must be thrown away. Salient designed a cartridge that easily opens by hand and snaps closed on all four sides. The N95-equivalent filter material can then be replaced or sterilized and reused. Salient’s previous experience designing many other various products allowed the Salient team to quickly respond and design a needed cartridge.
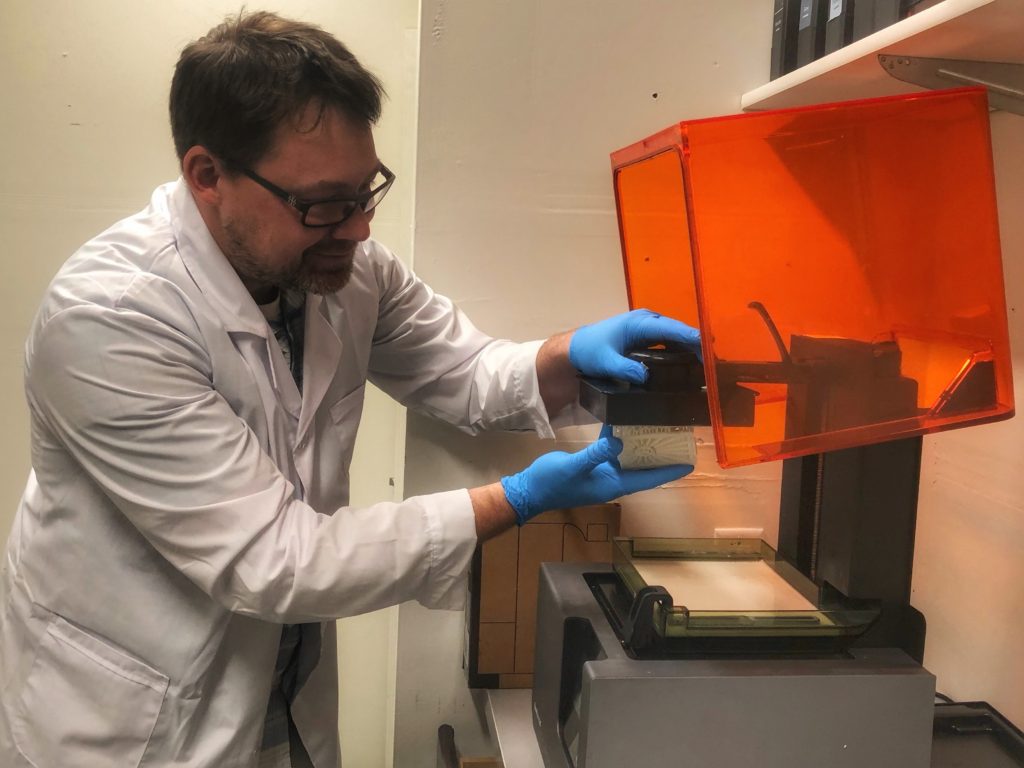
Salient is proud to collaborate with many other Montana entities in the effort to respond to COVID-19. As one of several companies that raised their hand to collaborate through the Montana Manufacturing Extension Center COVID-19 rapid response task force, Salient was appointed to oversee the design of the bayonet mount filter cartridges and compatible mask to ensure a quick and standardized response. Several injection molding shops around the state have expressed interest and are ready and willing to manufacture personal protective equipment for the state and beyond. Montana Tech is currently conducting testing on the Salient-designed filter cartridges to help validate the airflow as it moves through the certification process bringing it closer to full production.
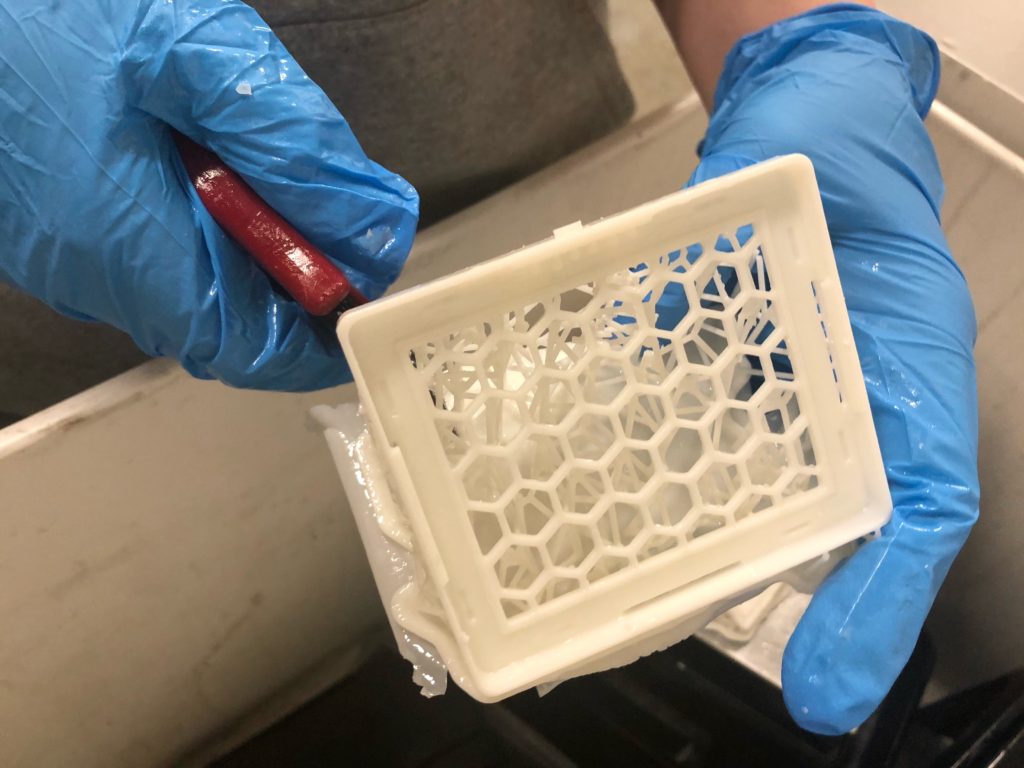